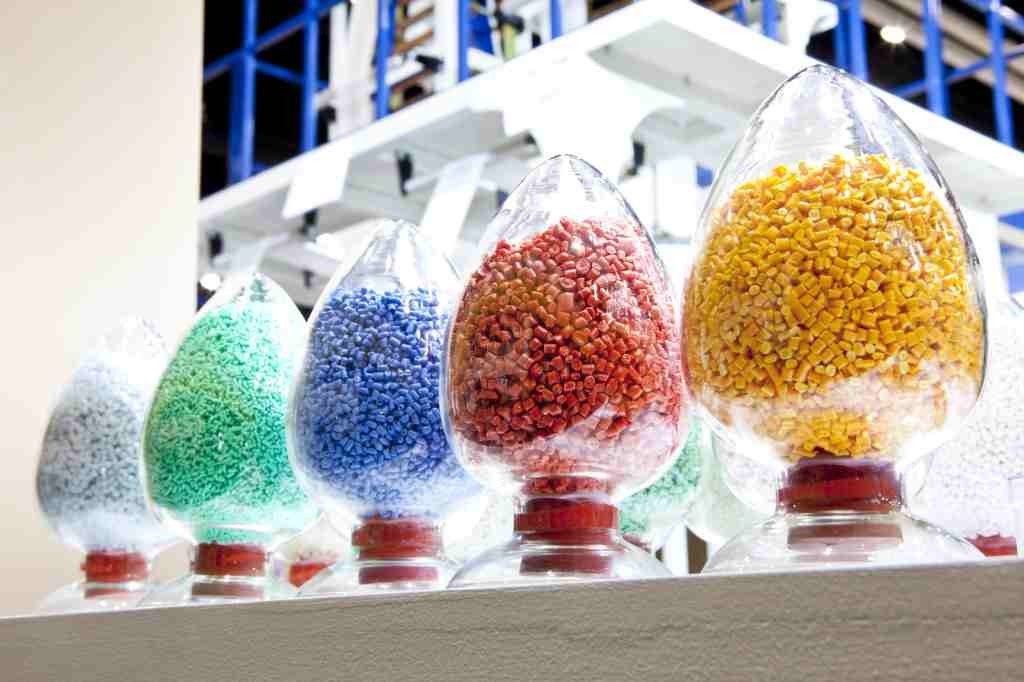
Our goal is to empower our customers to design and produce the best parts possible by providing them with the highest-performance and lowest-cost material to allow them to compete in their respective markets.
Ecomass Technologies has been delivering innovative solutions through advanced composite materials and engineered thermoplastics since 1998. We have a history of working with government and commercial customers to overcome physical property and material challenges to meet their application needs. Our experience and expertise in the formulation and development of high density thermoplastic compounds give our customers, original equipment manufacturers and material processors, the design freedom to focus on form and function, while we solve the material challenges their products face. Our goal is to empower our customers to design and produce the best parts possible by providing them with the highest-performance and lowest-cost material to allow them to compete in their respective markets.
HIGH DENSITY SPECIALIZATION
Specializing in high density and lead replacement applications, our high-gravity compounds can be formulated up to 11 g/cc and can be utilized in a wide array of applications, including weighting, balancing, radiation shielding and vibration damping. Moreover, all Ecomass Compounds meet the EU RoHS Directive, are 100% lead free, and do not contain any toxic constituents or material considered hazardous by the U.S. EPA. All Ecomass Compounds comply with Section 1502 of the Dodd-Frank Act.
APPLICATION VERSATILITY
Engineered to replace traditional materials, our high-gravity compounds have been used as a substitute for lead, aluminum, steel, stainless steel, brass, bronze, copper, and tungsten in a variety of applications. Ecomass high gravity compounds have been used to replace lead projectiles with nontoxic frangible projectiles used as training ammunition for military and law enforcement personnel. They have been used to shield numerous x-ray and gamma ray sources in medical and industrial devices. They are used to dampen vibration in direct customer-contact applications in the automotive and sporting goods industries, adding value customers can really feel. Moreover, they can be used as balancing weights to reduce the loads a part is exposed to, thereby increasing their service life. Our materials give you the density of traditional metallic materials with the production and economic advantages of injection or compression molding.
CUSTOM PRODUCTS, STOCK PRICING—LOW MOQ
The large number of base resins and weighting agents at our disposal give us the flexibility to engineer materials to meet our customers’ exact product and application needs at an optimal price point. Moreover, our experience and expertise in working with numerous base resins allows us to be completely objective when determining the engineered thermoplastic composite material best suited to deliver customer solutions. We truly work to help develop a material perfectly engineered for your application needs, as opposed to simply trying to sell you the closest approximation off the shelf. In other words, we work to engineer our materials to meet your application needs, instead of trying to engineer your application to meet our material properties. Moreover, while the industry trend has been to continue to raise the Minimum Order Quantity (MOQ) for non-standardized materials, we continue to maintain our 500 lb minimum order quantity, even for newly developed formulations, to demonstrate our commitment to providing customers with the best possible material to produce the best part.
PROCESSING
Some material processors express concern when attempting to run materials with high metal powder loading levels. Our high gravity compounds, however, are no more abrasive than 50% glass-filled nylons, which processors have been running successfully for 50 years. We factor processing considerations into every formula we develop and manufacture, and processing support is available and encouraged whenever trials of our materials take place. Our technical support personnel all have extensive experience in processing and are available for support whenever possible.
DESIGN
Our technical support team all have extensive experience working with customers to review their plastic part designs, both for functionality and processability. Our design expertise can help take your product from a concept sketch all the way to a finished part, and we are there to support you at every step along the way.
CUSTOMER SERVICE
Our customer service team is recognized by our customers for their experience and responsiveness. We try to stay as proactive as possible in all relationships with our customers to help us stay ahead of our customers’ needs.