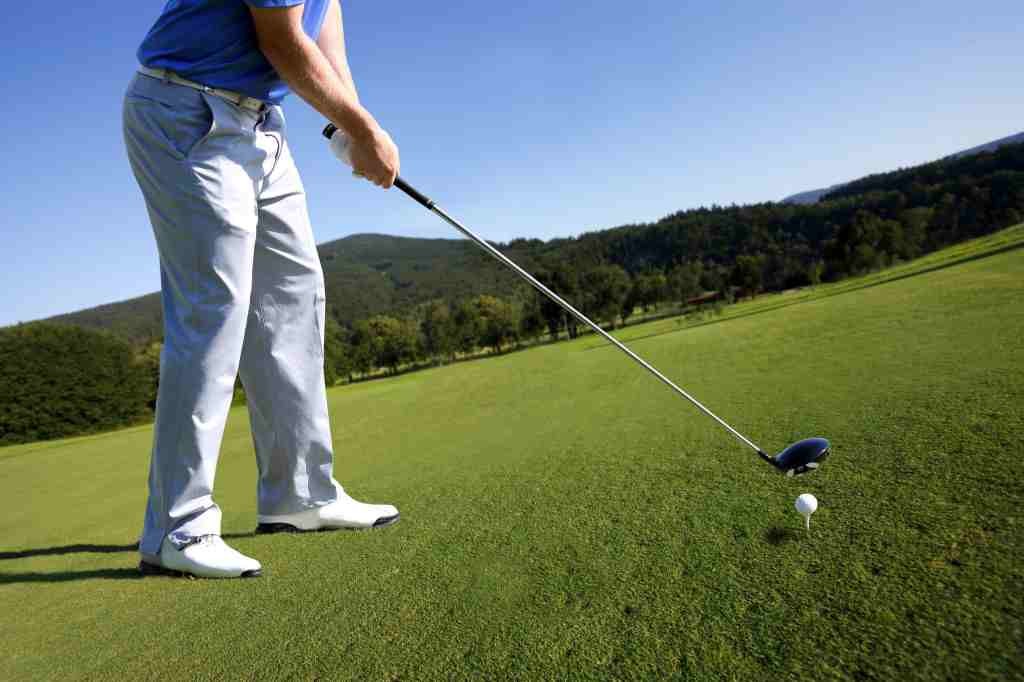
The wide density range of Ecomass high gravity compounds (up to 11 g/cc) give part designers additional design freedom by providing the weight of metals with the design and production advantages of injection molded plastics.
The need to place weight in precise amounts at specific locations has challenged designers for years. The ability to mold Ecomass high gravity compounds into small, intricate parts at any density from 2 to 11 g/cc makes these materials valuable to engineers and designers who want to replace lead and other traditional materials in order to eliminate toxic materials from their products and/or reduce costs.
Why Ecomass?
Due to their high density material offerings of up to 11 g/cc, Ecomass high gravity compounds deliver outstanding performance whenever designers require considerable weight in small spaces. Our high density injection-moldable materials can help free up premium space in component parts, giving part designers more design latitude and freedom. Moreover, our weighting and balancing compounds can be modified to satisfy a wide range of physical property requirements, such as tensile strength, impact strength, flex strength, flex modulus, and heat deflection temperature. Like the entire Ecomass Compound product line, our weighting and balancing engineered thermoplastics are RoHS compliant and are completely lead-free, designed to meet our customers’ ever-increasing needs for quality lead-free products and materials.
Our high gravity compounds have added value to a wide array of weighting and balancing applications, including:
- Nontoxic frangible projectiles
- Manual transmission shifter cartridge
- Hub odometer
- Instrument housing
- Golf club weights
- Inertia discs
- Return weights
- Casino Chips
Frangible Ammunition
Nontoxic frangible small-caliber training projectiles are an ideal application for Ecomass high gravity compounds. The use of Ecomass nontoxic frangible projectiles molded with either copper-filled or tungsten-filled compounds in small caliber rifle and handgun frangible ammunition improves safety by eliminating ricochet and lead contamination risks at firing ranges.
Customer Contact Applications
Weight can also be advantageous in certain customer-contact applications. In automotive manual transmission shifters, drivers appreciate the increased weight provided by Ecomass high gravity compounds molded into a cartridge which slides over the shift rod, in addition to the decrease in vibration transmitted through the shifter. This vibration damping improves product performance and service life, adding value that the end-user can truly feel.
Our high gravity compounds have also proven to be valuable in several golf applications. In order to fine tune the swing weight of premier golf clubs, designers have turned to Ecomass Compounds to provide the answer. These materials, molded into golf club weights, are installed in irons and wedges to allow customers to be fitted perfectly with the latest in golf club technology.
Replace Lead and Traditional Materials with Ecomass Compounds
Originally designed to replace lead with a nontoxic high density thermoplastic, Ecomass high gravity compounds are the perfect lead substitute, helping customers meet health and industry standards while overcoming ever-increasing regulatory concerns. Ecomass Compounds have replaced lead as a weight in a hub odometer used to monitor mileage on the trailers of semi-tractor-trailers. Our compounds have also replaced a lead and stainless steel housing used for ballast and protection of submerged water quality instruments. The compound selected meets all of the requirements for the housing, while reducing costs.
Small flywheels, also known as inertia discs, are another excellent application for Ecomass Compounds. Many electric and electronic devices use zinc, steel or lead inertia discs or weights which can result in corrosion issues. Moreover, if these products contain lead, they cannot be sold in the European Union. Our lead-free inertia weights at 10 g/cc provide the necessary weight with a minimum part size and can be a viable replacement for lead, zinc, steel and other traditional materials.
Similarly, Ecomass Compounds are used as return weights for kitchen faucets with pullout spouts. Previously, these weights were made of lead or die cast zinc. But a specially formulated injection molding grade Ecomass Compound weight replaced these traditional materials resulting in a superior product at a lower cost.
The elimination of lead in these product allows them to be sold worldwide, overcoming the regulatory concerns posed by countries which have banned the use of lead in such devices.
Contact Us Today
Follow the links below to learn more about Ecomass Compounds developed for weighting and balancing applications and their relevant case studies. Or, fill out our RFQ form or give us a call to learn how we can develop and deliver an engineered thermoplastic weighting and balancing material to meet your needs.