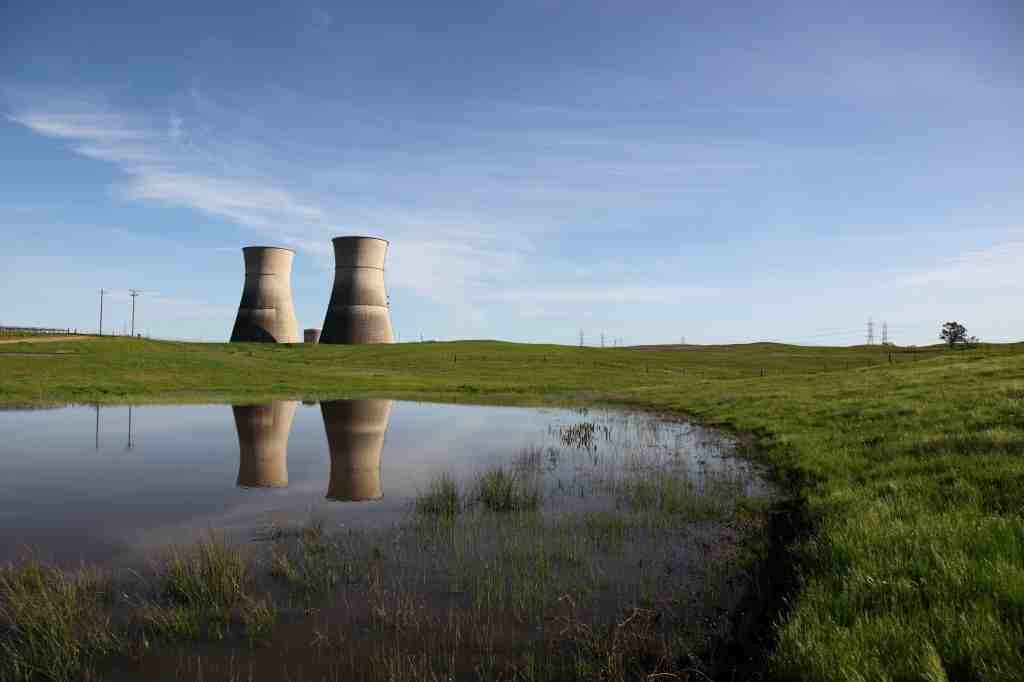
Ecomass Compounds are an ideal lead replacement material. Eco-friendly and injection moldable, our thermoplastic composites achieve the density of lead without any toxic concerns.
Ecomass Density Modified High Gravity Compounds – Quality Lead Replacement Materials
Ecomass injection moldable high gravity compounds are an ideal lead replacement material. Ecomass’ line of density modified high gravity compounds combine the design and production advantages of plastics with the desired density of metals. Our high density engineered thermoplastics and custom material formulation and development capabilities allow us to tailor the density — and subsequently mass— to your exact specifications and application requirements. Our high gravity compounds can be formulated up to 11 g/cc, the density of lead, and can be injection molded into complex shapes. Moreover, all Ecomass Compounds meet the RoHS directive, are 100% lead free, and do not contain any materials considered hazordous by the U.S. EPA. Ecomass’ lead replacement materials allow you to add mass where you want it, when you want it. Contact us today, or fill out our RFQ Form, to learn how we can formulate the optimal lead replacement material for your application. Or, check out our case studies page to learn how our high density thermoplastics have become a successful lead substitute for our customers.
Heavy Plastics?
One of the central appeals of thermoplastics has been their ability to make parts lighter and less expensive, while providing performance benefits over traditional materials such as glass, ceramics, aluminum, steel, zinc and lead. Given the general industry trends pushing for ever-lighter and stronger materials, the very concept of ‘heavy plastics,’ or high density materials—otherwise referred to as high gravity compounds—seems to contradict the fundamental advantages for which plastics became so popular. Despite these macro trends, part designers often enough run into situations and applications in which they need material to do just the opposite: rather than reduce weight, they need materials that add it. Whether the goal is to add weight to improve performance, balance assemblies to increase service-life, dampen vibration to enhance the customer contact experience, or shield radiation to improve safety, there are many applications in which designers and original equipment manufacturers need access to high density materials that allow them to add mass to specific locations. One important application responsible for the demand for such high density thermoplastics is the ever-increasing need for quality lead replacement materials.
Lead – Common, Useful and TOXIC
Lead is an extremely useful commodity, due mainly to its low cost and outstanding physical properties: high density, ease of fabrication and casting, and malleability. As a result, lead has grown to become useful in a number of widespread applications such as bullets, fishing rod sinkers, balancing weights for tires, and hunting shot, etc. In spite of its attractive properties and common usage, lead is a major environmental contaminant due to its toxicity. Lead is a toxic material that currently ranks number two on the U.S. Government’s Top 100 Hazardous Substances Priority List. Lead is toxic to humans and wildlife and creates significant environmental concern for disposal. Due to its toxicity, the regulatory environments, in the U.S. and Europe in particular, have grown increasingly strict regarding the use and disposal of lead. The U.S. EPA has set very restrictive thresholds limiting concentrations in air, soil, water and vegetation. Moreover, limitations on the use of lead have been set in unleaded gasoline, paint, and general exposure in the workplace. As a result, the need for an environmentally friendly lead replacement material that can be formed into complex shapes has become increasingly important.