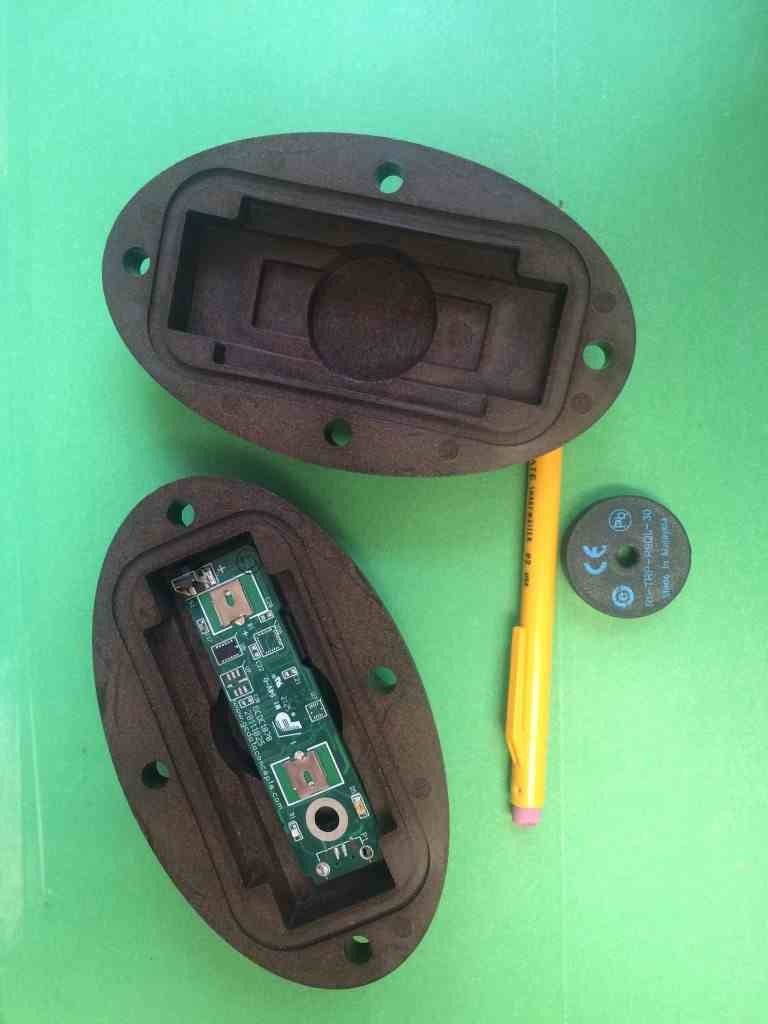
The University of Texas at Austin Jackson School of Geological Sciences turned to Ecomass Technologies to develop an innovative and practical lead free solution for their Smart Rock sensor. Smart Rocks are intended to mimic the behavior of typical river rocks during high flow conditions to help researchers better understand the effects of flash flooding and sediment flow in Texas rivers and streams.
Challenge:
Smart Rocks are similar in weight and shape to ordinary river rocks, but have an internal cavity that contains small electronic instruments designed to capture various data including acceleration and motion, along with an RFID identification chip to assist in retrieval. Smart Rocks are distributed along streambeds where they lie until a flash flood that is large enough to move the three inch sensor. The Smart Rock is then retrieved and the data collected.
Previously, researchers at UT had been using concrete cases for their Smart Rocks, however, these prototypes limited the field life of the Smart Rock considerably as the cases could not be reopened and closed as was required to change the batteries. They then moved to plastic cases and used lead weights to achieve the desired bulk weight of the rock, but the lead interfered with RFID transmittal, making data retrieval more difficult. To overcome these challenges, researchers sought a lead free solution that could deliver the density of the rock while safely housing their electronics without interference.
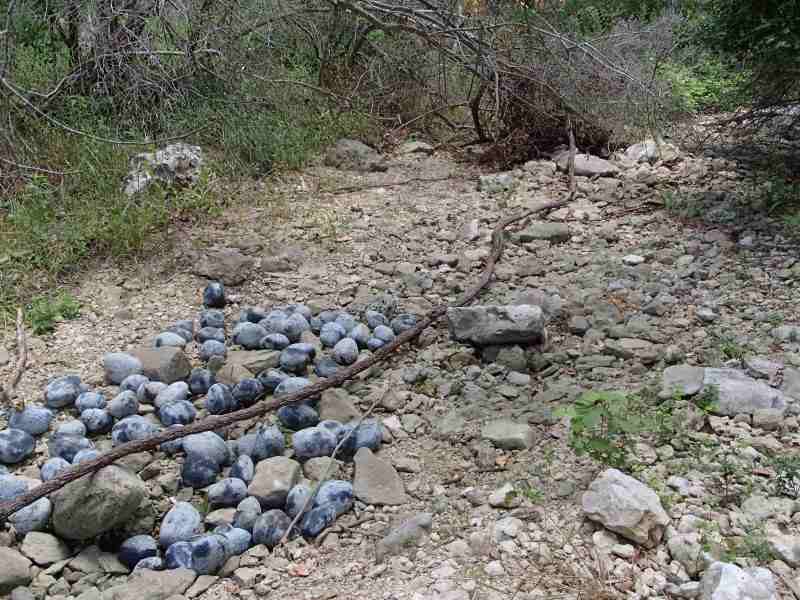
The Ecomass Solution:
Ecomass Technologies helped to develop an injection molding grade copper powder filled PA12 alloy at 3.3 g/cc with good toughness (Ecomass Compound 1050CO78) specifically for this application. Ecomass Technologies assisted in the material evaluation process by supplying injection molded sample plaques that researchers used to evaluate machinability and to determine whether the RFID signal could be effectively transmitted through the material. Ecomass also assisted in the process by developing a CAD prototype which was used to 3D-print prototypes to test the Smart Rocks for fit and function of the instruments housed inside. Ecomass recommended a symmetrical part concept such that only one mold was necessary, thereby cutting initial projected molding costs in half. Weighing just over two pounds, the final Smart Rock design includes a cavity for the electronics package with an O-ring and four external bolts to achieve a waterproof seal.
This case study demonstrates the versatility and the value that Ecomass Technologies can add to the design, development, and manufacturing processes. Ecomass works to identify and develop the ideal material specific to each and every application, assisting the customer every step of the way from material development and part design, to product delivery.