Introduction
The use of lead in many products and devices poses certain health risks and environmental concerns. A new line of nontoxic, high density, polymer-metal composites, trademarked as Ecomass® Compounds[1], can replace lead and many other traditional metallic materials in a variety of application areas including weighting, balancing, vibration dampening, and radiation shielding. These composite materials are custom formulated to provide a wide range of physical properties and are designed to process on conventional injection molding, compression molding, and extrusion equipment. These materials meet some of the most demanding requirements in industries such as defense, power generation, medical, automotive, and sporting goods.
Manufacturers are constantly striving to make their products safer and easier to recycle while governmental agencies are encouraging such actions by continually increasing the restriction of the use of hazardous materials in consumer and industrial goods. Nontoxic polymer-metal composite materials provide an efficient and cost effective way to eliminate hazardous materials like lead (ranked No. 2 on the U.S. EPA’s Top 20 Hazardous Substances Priority List). Companies processing as little as 100 lbs. of lead are now required to file annual reports under EPA’s Toxics Release Inventory (TRI) program.
At present, more than forty distinct high density composite materials are available as commercial products with a similar number under development. To meet individual customer needs, these composites can be custom-formulated across a wide range of densities (2.0 to 11.0 g/cc), impact strength, tensile strength, flexural modulus, and heat-deflection temperature. Parts molded with Ecomass® Compounds have successfully replaced parts previously manufactured with aluminum, stainless steel, brass, bronze, zinc, and copper, as well as lead.
Ecologic, toxicologic, AND ECONOMIC implications
Because of its cost, mass, and radiation shielding capability, lead has traditionally been used in a variety of applications where these attributes are beneficial. Offsetting these benefits are lead’s poor mechanical properties and the fact that lead (including its oxides and compounds) is toxic, a characteristic that has been known since antiquity[2]. Lead usage has been restricted since the late 19th Century and is now virtually prohibited in cases of direct human or animal contact by increasingly stringent regulations and laws.
Lead has been banned as an additive in motor fuels, in paints, and in water pipes. Its use is restricted as shot in migratory waterfowl hunting and as fishing tackle in three states and most of Europe. The European Union has banned the use of lead automobile wheel weights and, with its RoHS Directive (2002/95/EC), has restricted the use of lead and five other hazardous materials in electrical and electronic equipment. Increasingly, regulatory burdens, handling costs, and disposal costs are impacting every use of lead, including uses in the automotive, aerospace, consumer goods, medicine, nuclear power generation, and sporting goods industries.
The state of California requires public notification of hazardous substances in products produced or shipped into the state under California Environmental Protection Agency Regulation 65. Lead compounds and lead acetate are included in the list of hazardous substances. Historically, such action by California has preceded similar action by other states and the United States on a national scale.
Ecomass Technologies has developed a line of nontoxic composite materials which can replace lead in numerous applications, thus reducing the quantity of this toxic metal that is ultimately discarded and finds its way into our landfills – potentially contaminating the drinking water supply. These polymer-metal composites, comprised of various thermoplastic resins and nontoxic metal powders, are patented and marketed under the name Ecomass® Compounds. These materials offer engineers and part designers more freedom to develop parts and products that meet their needs by eliminating traditional constraints related to the specific gravity and other mechanical properties of certain metallic materials and limited forming processes.
Although these composite materials are generally more expensive than metallic materials of the same density on a pound for pound basis, they can be an economically viable alternative due to their inherently low processing costs resulting in a total manufactured part cost that, in many cases, can be less than that of traditional metallic materials[3].
Material PROPERTIES
These new materials pose no toxic or ecological threat and can be successfully recycled during initial processing and at the end of a product’s useful life.
Different choices of polymeric binders and types of fillers yield compounds with densities ranging from 2.0 g/cc to 11.0 g/cc (the same density as the typical lead alloy). It is in the higher density forms that the new composites are similar in behavior to the heavy metals, primarily lead, but also lead alloys, zinc, brass, silver, bismuth, molybdenum, and solid tungsten. Work is currently underway to increase filler loading levels, and thus material density, while maintaining acceptable physical properties.
Selected data for 7 injection molding grade materials consisting of 2 resin systems (materials 1 – 3 and materials 4 -7) with various filler levels and densities from 5-11 g/cc appear in Table I.
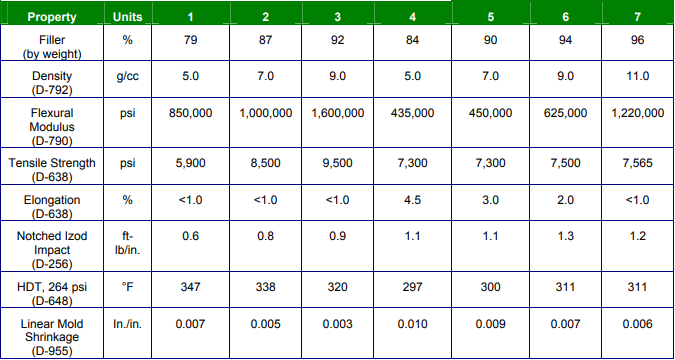
Table I – Selected characteristics of 7 composite materials which vary by % filler and resulting density.
Health and Safety Hazards
One of the primary filler components of these composite materials, tungsten powder, was selected for its density, and overall lack of reactivity and toxicity[4]. Other nontoxic metal and non-metal powder fillers used in these materials include aluminum, carbonyl iron, barium ferrite, barium sulfate, stainless steel, and copper. The polymer components of the composites consist of resins long approved for consumer products, food contact and medical applications. These base resin systems include polyamides (PA), co-polyamides (COPA), polyurethanes (TPU), polyethylenes (PE), polymethylpentenes (PMP), polyetheretherketones (PEEK), polysulfones (PSU), acrylonitrile butadiene styrene (ABS) and styrene ethylene butylene styrene block copolymer (SEBS).
One form of the material has met the requirements of ISO 10993-5: In Vitro Cytotoxicity Study for Biocompatibility. Material Safety Data Sheet (MSDS) information developed for the new materials details the absence of any toxic or health hazards. Critical parameters are as follows:
- Not classifiable as toxic waste if spilled or leaked as supplied
- Insoluble in water
- No unusual fire or explosion hazard
- Flash point of >400°C
- Extinguishable with any cooling or oxygen-excluding method
- No health hazard threshold limit value; product is inert
- No carcinogenic agents
- Stable in terms of reactivity (is incompatible with strong oxidizing agents and fluorine gas)
- No respiratory protection is required; gloves and eye protection are routinely recommended during processing
In addition, these composite materials would not be classified as a Mixed Waste if contaminated by a Radioactive Waste.
Density
The ability to tailor the density of these nontoxic composites to meet the needs of customers with a thermoplastic solution that can replace metallic materials, and (in the case of lead) a toxic/hazardous material, is the greatest attribute of these materials. Being able to formulate and manufacture these composites with acceptable physical properties at very high filler loading levels is the challenge that has been met and overcome.
Figure 1 compares the maximum composite material density with those of traditional metallic materials. Parts made with these composite materials at a density of 11 g/cc can be used as a direct replacement for lead parts. They can also be used to replace parts previously made with lower density metallic materials thereby reducing the part volume and saving space in critical applications.
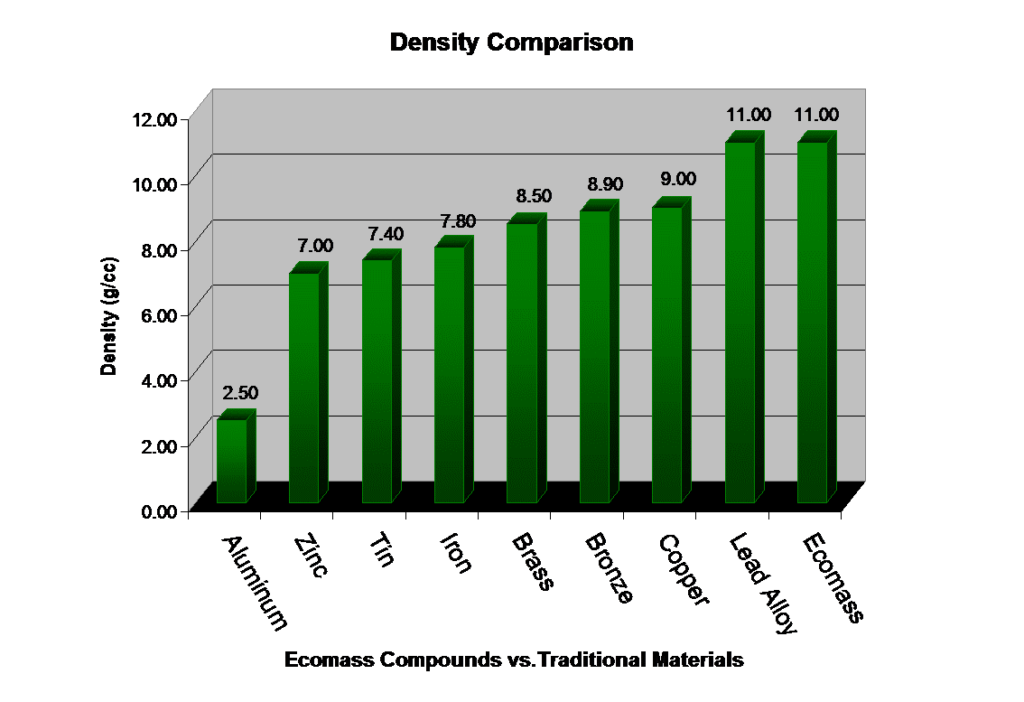
Figure 1 – Comparison of the maximum density of the new composite material with those of common metals. The new polymer-metal composite’s density of 11 g/cc matches that of generally available lead alloy.
The effectiveness of radiation shielding is to a large extent determined by a material’s density, radiation absorption of the filler materials (in the case of a polymer-metal composite material), and molecular or crystal structure. The 11.0 g/cc composite materials have been developed to approximate the shielding properties of lead and testing by Texas A&M University has confirmed their ability to shield common forms of radioisotopes, gamma radiation, and x-rays[5].
Radiation Shielding
Table II lists the radiation shielding capabilities, in relation to lead, of the new composite material at a density of 11.0 g/cc. In this table, the shielding performance of lead equals a value of 100. A useful design feature is that by using a correspondingly thicker wall or layer of the new composite material, almost any shielding requirement can be achieved.
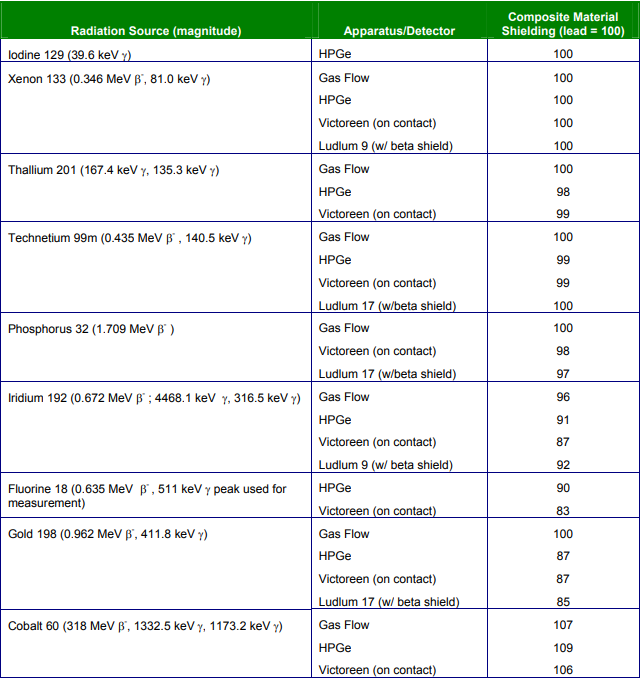
Table II – Radiation shielding of new composite material at 11.0 g/cc vs. lead (lead = 100)
Applications
The primary application areas for these materials identified to date are weighting, balancing, vibration/sound dampening, and radiation shielding. Current applications include:
Weighting
- Projectiles in military ammunition
- Projectiles in law enforcement ammunition
- Aircraft fuel shut-off valve weights
- Cable sheathing
- Golf club head and shaft weights
Balancing
- Automobile wheel weights
- Automotive speedometer needles
Vibration/Sound Dampening
- Military and civilian headphones
Radiation Shielding
- Reactor shielding
- X-ray tube housings
- Chemical imaging agent shielding
- Collimators
- Radioisotope containers
- Lead-free shielding tape/pipe wrap
- Technician and patient shielding
Injection or compression molded into virtually any custom three-dimensional geometry and wall thickness, these high density composite materials can provide weighting, balancing, vibration dampening, and radiation shielding for even the most tightly constrained, space-conscious application; a benefit for engineers and designers who must contend with ever-shrinking product footprints. Other applications can use the materials in a sheet or film form. Extrusion grade materials that can be processed into sheet and tape have found uses in nuclear power plants as a pipe wrap to reduce employee dose rates in high traffic areas.
Finally, by fine tuning the mechanical properties of these materials, a significant reduction in substrates and support assemblies can be realized. The result is that designs can be developed with fewer components and, where lead was once employed, manufacturers and end-users can bypass the expense, special procedures, legal liabilities, documentation, and regulatory pressures associated with the use of lead.
Conclusion
A new line of nontoxic, high density, composite materials, Ecomass® Compounds, is now available to engineers and designers for use in weighting, balancing, vibration dampening, and radiation shielding applications. These materials, consisting primarily of thermoplastic polymers and nontoxic metal powders, can replace lead and other traditional metallic materials in a cost effective manner by offering improved physical properties and processability on conventional molding and extrusion equipment. These materials represent an ecologically and economically sound alternative to traditional materials that are, in many cases, becoming increasingly environmentally undesirable.
Notes and refErences
- The manufacture and sale of Ecomass® Compounds are licensed by Ecomass Technologies (Austin, Texas) to Technical Polymers LLC (Buford, Georgia) and are protected by S. and international patents. Additional information available at www.ecomass.com.
- Lansdowne, R. and Yule, W. editors, Lead Toxicity: History and Environmental Impact, Baltimore, Johns Hopkins University press, 1986. Also, Nriago, J.O., Lead and Lead Poisoning in Antiquity, New York, 1983.
- X-ray Manufacturer Gets the Lead Out, a case study at ecomass.com.
- Tungsten has the highest melting point of all elements except carbon, at 3,400°C, with good high-temperature mechanical properties and the lowest coefficient of expansion of all metals. With a density of 19.25 g/cc, it is among the heaviest metals. Primary uses include hard metal alloys (including tungsten carbide), steel alloying, incandescent lighting filaments, electrical/electronic contacts, wire, and rod. The name itself is of Swedish origin: tung (heavy) and sten (stone), in deference to the Swedish chemist/mineralogist who first discovered and described the ore. It is also known as wolfram, which gives tungsten its chemical symbol, W. (Source: Tungsten Industries Association [London]).
- Report dated August 13, 1998 of tests performed at The Nuclear Science Center, Texas A&M University, College Station, Texas. Complete results at ecomass.com.
Contact:
Robert Durkee
Ecomass Technologies
4101 Parkstone Heights Drive
Suite 380
Austin, Texas 78746
U.S.A.
512.306.0020
durkee@ecomass.com
www.ecomass.com